Enhancing robot and machine safety
Ensuring safe interaction between industrial robots and their operators is an essential part of a high-functioning integrated system.
At Shell-O-Matic, we work with the ANSI/RIA R15.06 (Industrial Robot and Robot Systems Safety Requirements), ISO 10218 (Safety requirements for industrial robots) and ISO 12100/ISO 13849 (Safety of Machinery) guidelines to provide comprehensive safety solutions specific to our customers’ needs.
Three-step process:
- Generating a risk assessment matrix of your machinery, as required by the relevant standards
- Analyzing all interactions between humans and machines
- Providing risk-reduction strategies
Dynamic control of robot working envelop
Controlling the robot’s working envelop (its reach) is the first step to creating a dynamic and safe collaboration between the robot and an operator.
Robot manufacturers offer software options to dynamically control the robot working envelop as a function of system status.
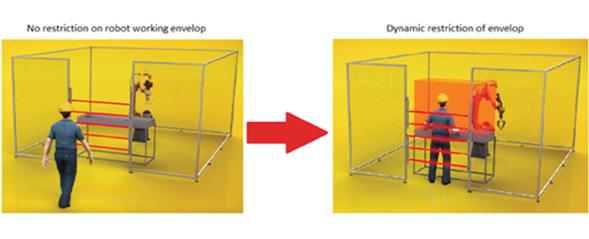
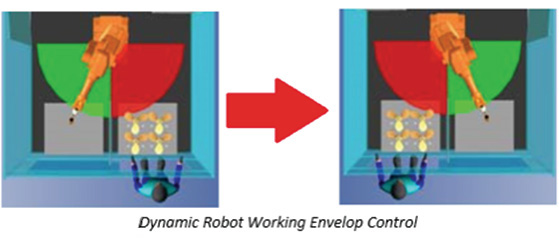
Programmable safety controller
An optional part of the Shell-O-Matic Supervisory system, the programmable safety controller allows for more complex safety logic.
Advantages of the programmable safety controller:
- Manage the various safety devices and functions required with a robotic cell
- Scalable
- Reprogrammable, so it can evolve the logic or system with changing customer needs
- Communicates at the machine network level
- Share safety system status
- Adjust PLC control logic
- Display appropriate messages on the HMI screen
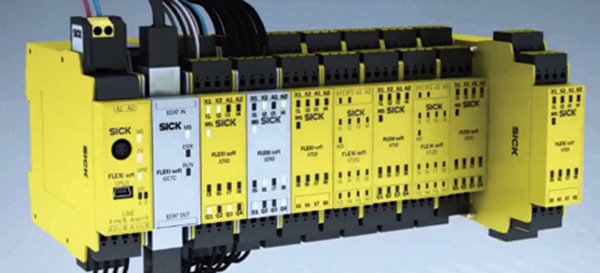
Safety devices
Shell-O-Matic can create a custom safety system tailored to customer needs. The system can be connected to various safety devices, including:
- Light curtains
- E-stop buttons
- Two-hands controls
- Area scanner
- Safety mats
This system allows Shell-O-Matic to deliver not only a new state-of-the-art safety system, but also to retrofit or upgrade existing robotic cell safety systems.
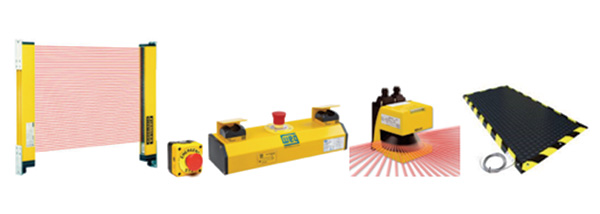